
So it can only be filled with liquid nitrogen. However, these materials cannot be vacuumed and need internal pressure to prevent deformation. To reduce costs, save energy, and improve convenience, nowadays tinplate cans are being replaced by pop-top aluminum cans and plastic bottles/cans. Vacuum pumping has a slower production speed, while the vacuum formed by steam injection requires hot filling. Connecting the vacuum chamber of the can seamer to the vacuum pump or steam injection are the common methods used, but they have some limitations. In the food and beverage industry, achieving a vacuum in packaging containers can be challenging. Preservation of Organic Product Quality – No need for preservatives to extend shelf life.Low Oxygen Function – Inert gas packaging helps maintain product freshness.Elimination of Deflated Bottles/Cans – Increases bottle pressure to eliminate flatness issues.Bottle Durability – Maintains the original shape of lightweight bottles.Easy Labeling – Consistent bottle hardness improves labeling efficiency.Replacing Glass with Plastic Packaging – Eliminates the health hazards and weight associated with glass bottles.Extended Shelf Life – Oxygen content is reduced to a lower level, resulting in longer shelf life.Light weighting of PET Bottles – Reduces the weight of PET bottles, saving costs and promoting environmental protection.The liquid nitrogen dosing machine has the following benefits used in the liquid food and beverage field: This extends the shelf life of the product, maintaining its quality and flavor over time By injecting a small amount of liquid nitrogen into the container(metal cans or PET bottles)before it is sealed, the oxygen is displaced, preventing oxidation and microbial growth. In the food and beverage industry, liquid nitrogen dosing systems are commonly used to preserve the quality and freshness of products such as coffee, beer, wine, milk, snacks, water, fruit jam or sauce and juices.
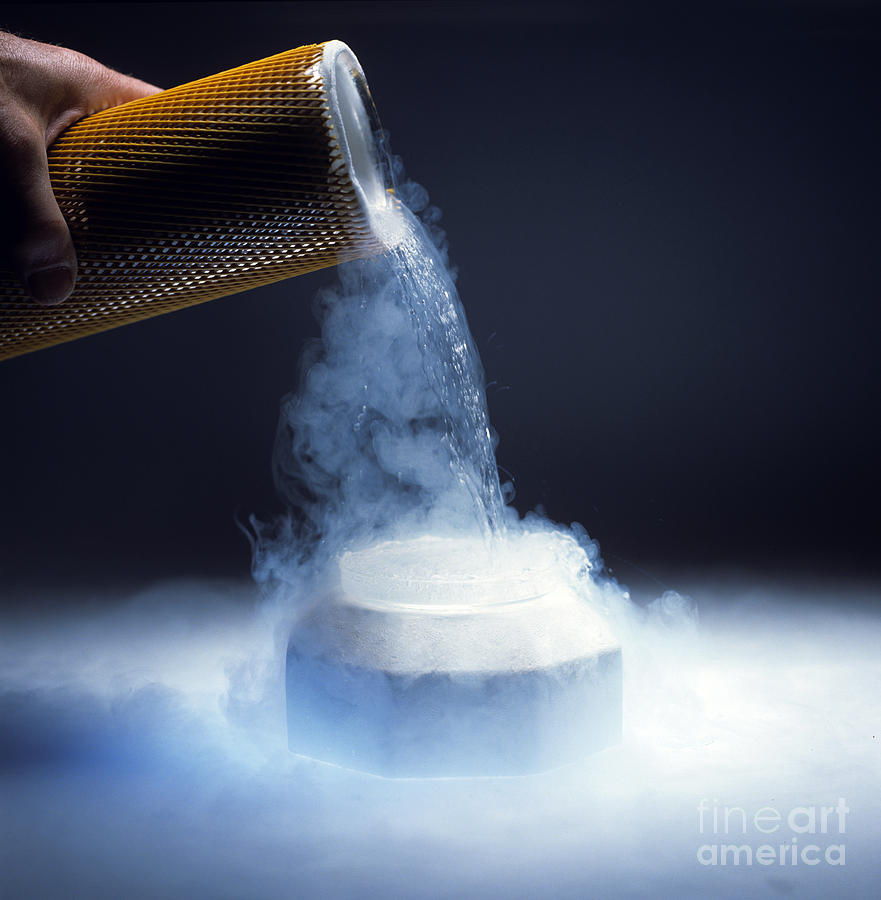

Fruit Vinegar And Fruit Wine Beverage Processing Line.
